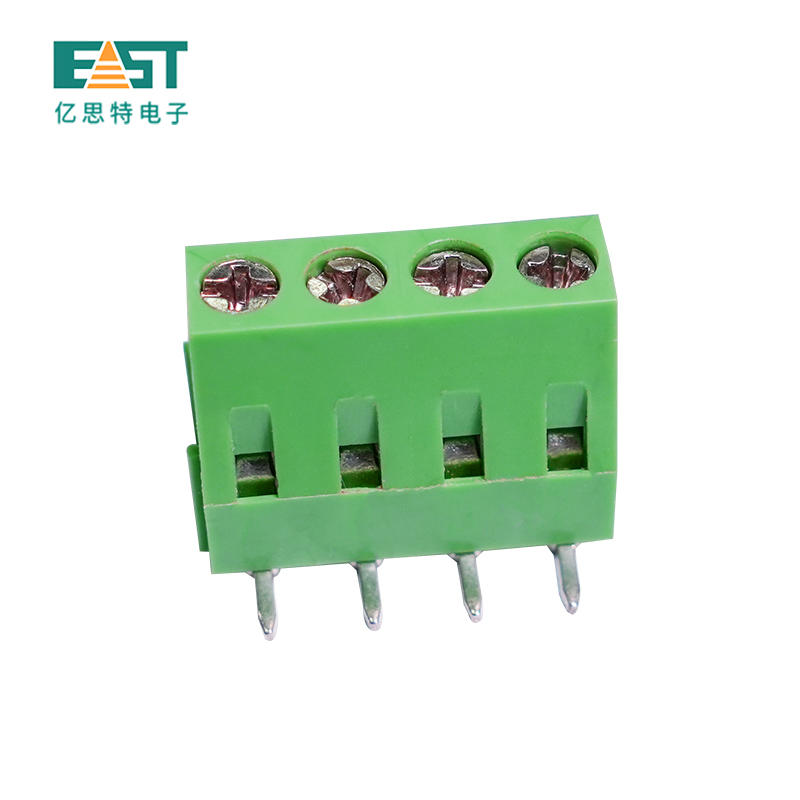
MX128R-5.0 5.08 Screw terminal block right angle height 14.3mm
Pitch:5.00/5.08mm
View moreThe safety of electrical connections largely depends on the correct installation and use of terminal blocks. As a key component for connecting wires in electrical systems, the fixing method, selection, and daily maintenance of terminal blocks directly affect the stability and safety of the system. Improper installation or insufficient maintenance may lead to serious consequences such as poor contact, short circuit, overheating, and even fire.
The installation of terminal blocks must be firm and reliable. In industrial automation, distribution cabinets, or control systems, terminal blocks are typically installed using DIN rail mounting. When fixing, ensure that the guide rail is flat and free of deformation, and use appropriate buckles or screws to lock the terminal block to prevent loosening due to vibration or external forces. If the terminal block is not fixed properly, it may shift during operation, causing wire detachment or poor contact, which can lead to equipment failure or safety hazards. Before wiring, it is necessary to confirm that the power supply has been disconnected to avoid the risk of electric shock caused by live operation.
Choosing the appropriate type of terminal block is crucial for improving safety. Common terminal blocks include screw type, spring type (such as push in), fence type, and insulation puncture type. Screw type terminal blocks are suitable for high current applications, but regular checks on fastening are required; Spring type terminal blocks are easy to connect and have strong anti vibration capabilities, suitable for environments with frequent vibrations; The insulation piercing terminal block is suitable for situations where fast wiring but low current is required. The material of the terminal (such as tin plated or silver plated copper alloy) and insulation material (such as PA66 flame-retardant plastic) should also be considered to ensure long-term stability and fire resistance.
Proper operation during the wiring process can effectively reduce the failure rate. When stripping, professional wire stripping pliers should be used to ensure that the exposed length of the wire is appropriate (usually 8-10mm), avoiding short circuits caused by excessive length or poor contact caused by insufficient length. Multi strand wires should be crimped or soldered to prevent loose wires from causing short circuits. Only one wire is allowed to be connected to each wiring hole to avoid increased contact resistance and heating caused by multiple wire compression. Exposed metal parts should be protected with heat shrink tubing, insulating tape, or terminal sleeves to prevent accidental contact from causing short circuits or electric shocks.
Regular inspection and maintenance are key to ensuring long-term safe operation. Due to factors such as temperature changes, mechanical vibrations, or corrosion, the fastening state of the terminal block may gradually deteriorate. It is recommended to check for loose wiring and oxidation or burn marks on terminals every 3-6 months. For high temperature, high humidity, or corrosive environments, gold-plated or silver plated terminals can be used to improve corrosion resistance and increase inspection frequency. If abnormal phenomena such as cracking of the plastic shell of the terminal block, discoloration of metal parts, or melting of the wire insulation layer are found, they must be replaced immediately.
Reasonable wiring design can also enhance safety. Avoid mixing high current wires with small signal wires on the same terminal block to prevent electromagnetic interference. The strong and weak current terminal blocks should maintain sufficient spacing (such as 20cm or more), and isolation boards should be installed if necessary. For analog signals that are susceptible to interference (such as thermocouples, PT100), it is recommended to use cables with shielding layers and ground the shielding layer at one end.